In an industry that thrives on stability and predictable pricing, few announcements have caused as much stir as the recent U.S. 25% steel tariff on steel and aluminum products set to take effect on March 4, 2025. For individuals and companies that design, manufacture, or utilize metal buildings, this news marks another significant point in an already dynamic pricing environment.
Rising costs for steel—combined with inflationary pressures on other inputs—have prompted many suppliers and fabricators to signal upcoming price adjustments, and it’s clear that the broader industry must brace for uncertainty and potential additional increases in the near future.
As a leading customer PEMB supplier, SteelCo has received notices from various metal building vendors and fabricators that they are planning to enact a 10-12% price increase in the couple of weeks, with another price hike around 10-12% some time in March.
In this industry news article, we’ll provide a big-picture view of how these 2025 steel tariffs, possible anti-dumping rulings, and coil-coating expenses will affect metal building prices. We’ll also offer strategic insights on managing risk, maintaining growth, and maintaining customer trust in an era defined by rapid changes.
Table of Contents:
- Setting the Stage: Tariffs, Sanctions, and Beyond
- The Ongoing Evolution of Metal Building Pricing
- Macro Trends Impacting the Metal Building Sector
- Strategies for Coping with Rising Steel Prices
- Practical Tips for Personal and Business Buyers
- Looking Ahead: How 2025 Could Shape the Future
- Conclusion
Setting the Stage: Tariffs, Sanctions, and Beyond
Steel Tariffs Announced for 2025
The Trump administration’s move to impose a 25% global tariff on all steel and aluminum products marks a stark departure from targeted tariffs of the past. While earlier measures often focused on specific countries accused of dumping steel, this wide-reaching policy applies to any source market. As a result, domestic steel producers may suddenly be less constrained by foreign competition, which could embolden them to raise prices. For end users—particularly those reliant on steel for large-scale building projects—the direct outcome is a likely uptick in overall project costs.
Fact Check: According to the World Steel Association (cited for global steel insights), the United States has historically imported over 20 million metric tons of steel annually. A global tariff could reshape these import dynamics overnight.
The Anti-Dumping Backdrop
Compounding the tariff question is an ongoing anti-dumping investigation reportedly involving ten different countries. If the authorities rule that these nations have indeed been selling steel at unfairly low prices, additional sanctions or duties could follow, restricting imports further or raising their cost. For companies that already struggle to find competitively priced steel, this scenario may lead to even higher input costs and potential supply shortages. The Office of the United States Trade Representative provides regular updates on trade actions and investigations, which can significantly influence how much steel is available—and at what price.
Coil-Coating Cost Inflation
Another piece of the puzzle involves coil coating, a pivotal process that gives metal building panels their corrosion resistance and aesthetic finish. Coil-coating materials—ranging from specialized paints to treatment chemicals—are already subject to inflationary pressures. Coupled with tariffs that make steel coil more expensive in the first place, coil-coating costs could escalate, sending ripples through every product that relies on these treated panels. Industry analysts at Grand View Research forecast that the coil-coatings market could see compound annual growth rates of over 5% through the mid-2020s, driven by both rising material costs and expanding construction needs.
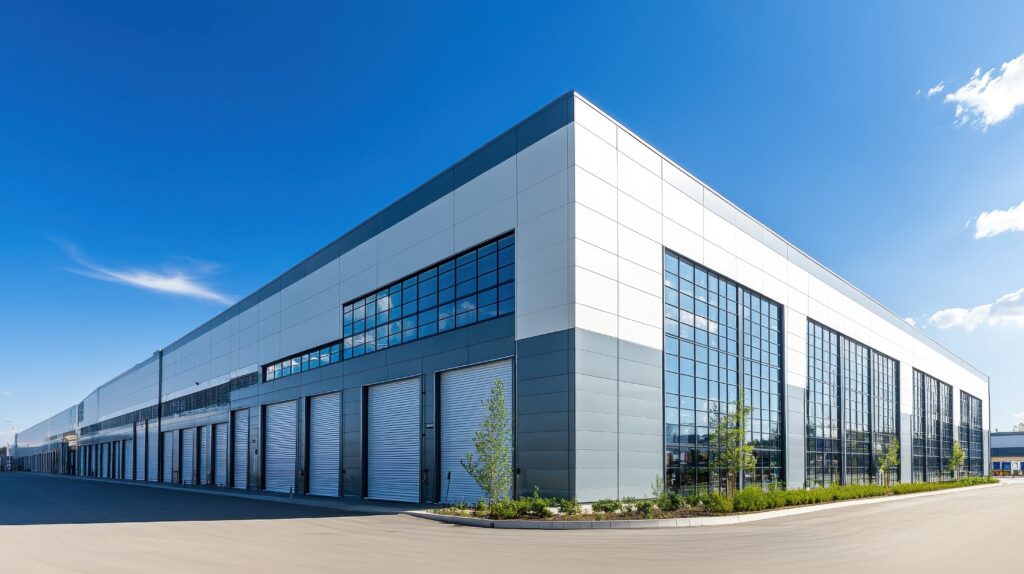
The Ongoing Evolution of Metal Building Pricing
Immediate Price Adjustments
Many metal building suppliers, anticipating a surge in steel costs, have preemptively announced price increases of their own—often in the range of 5–10%. Some have publicly stated that additional hikes may follow, given the volatility in raw materials and the uncertain geopolitical climate. These immediate adjustments allow companies to manage risk but also challenge customers to either lock in current prices or revise budgets as new quotes roll out. Recent Bureau of Labor Statistics reports show that steel mill products and related construction materials have experienced double-digit percentage increases in certain quarters, reflecting how swiftly market conditions can shift.
Further Inflationary Pressures
While steel tariffs grab headlines, inflation in general has been on the rise in 2025. Energy, transportation, and labor costs have all ticked upward, creating a chain reaction that can push metal building prices even higher. For instance, in logistics, elevated fuel expenses and driver shortages can lead to surcharges—costs that suppliers may pass on to end users. If the pace of inflation remains high or accelerates further, the cost of constructing metal buildings could stay elevated for the foreseeable future.
A Fluid Policy Environment
It’s important to note that the situation is far from static. Tariffs can be modified, repealed, or extended based on changing political winds. Anti-dumping cases may conclude in ways that either mitigate or amplify the impact on steel imports. Keeping up with policy developments is critical for companies trying to optimize their supply chain strategies, negotiate better deals, or time their purchases effectively. The American Iron and Steel Institute regularly publishes policy updates and their potential impacts on the U.S. steel market, providing valuable insights for both manufacturers and end users.
Macro Trends Impacting the Metal Building Sector
- Shifts in Domestic Production
As tariffs reduce the volume of imported steel, domestic producers often ramp up output to meet demand. While this can create opportunities for local mills, it can also invite new labor and overhead costs if capacity needs to expand quickly. Sudden ramp-ups can also lead to production inefficiencies or backlogs that delay project schedules. - Geopolitical Tensions
Trade relations have become increasingly complex in recent years. If more tariffs or sanctions emerge from other disputes, steel costs could remain volatile. Conversely, improved relations or trade deals might soften the impact, so it’s essential to monitor global events. - Push for Sustainable Solutions
Despite cost pressures, the demand for eco-friendly, energy-efficient buildings continues to rise. Innovations in steel manufacturing—including recycled content and reduced-carbon processes—might ease some price volatility over the long term. However, in the short run, sustainability initiatives can add to costs unless carefully managed.
Sustainability Insight: According to the National Institute of Building Sciences, sustainable construction methods can reduce long-term operating expenses but often involve higher upfront expenditures—something to consider if budget constraints tighten with rising steel prices.
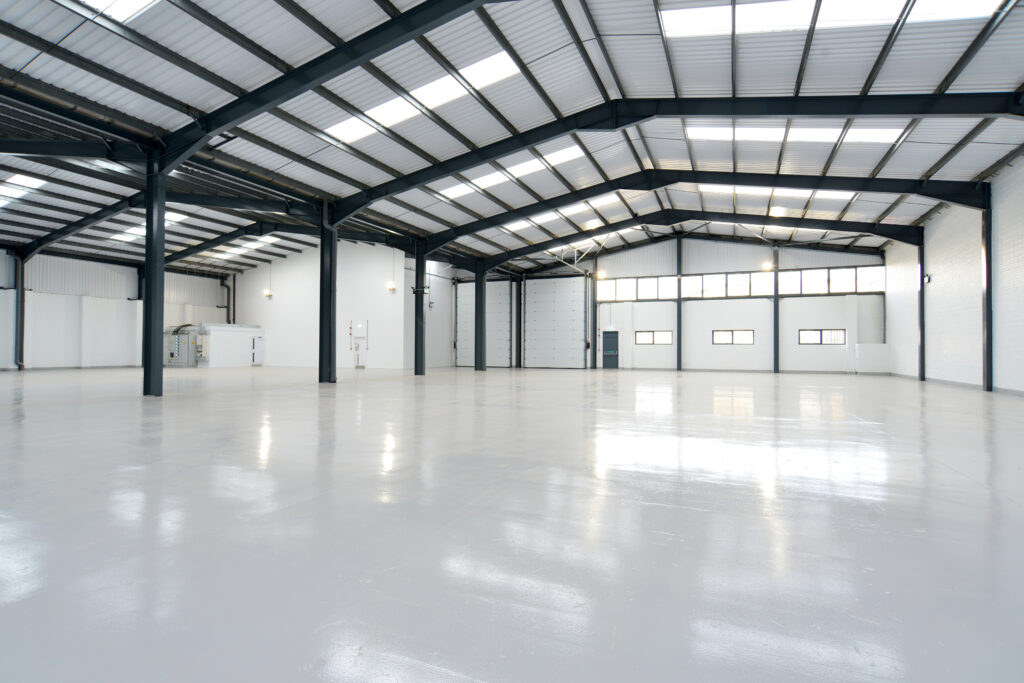
Strategies for Coping with Rising Steel Prices
1. Lock In Early Where Possible
Securing your steel requirements before the tariff officially takes effect or before further price escalations can save money. Though it’s not always feasible to pre-purchase large quantities of steel, even partial orders for critical components can hedge against future increases.
2. Revisit Building Designs
To offset rising metal building prices, consider more efficient designs that reduce the steel required. Architectural tweaks—like fewer interior columns or simplified roof geometries—may lower material usage without compromising functionality. Evaluate the trade-offs between aesthetics, structural demands, and cost savings.
3. Explore Value Engineering and Alternative Materials
In some cases, partial substitutions (e.g., certain cladding materials, composite beams, or reinforced concrete elements) may complement steel to form a hybrid solution. Though it won’t eliminate the need for steel, these choices can lessen the overall steel footprint and potentially mitigate tariff-based cost increases.
4. Plan Long-Term and Remain Agile
Given how quickly the market can swing, adopting a flexible approach is vital. Keep an eye on global trade developments, consider escalation clauses in your contracts, and maintain open communication with engineers and suppliers so you can pivot if new tariff announcements or sanctions alter your baseline costs.
Practical Tips for Personal and Business Buyers
Whether you’re an individual planning to build a barndominium or backyard workshop, or a business looking to construct a warehouse, distribution center, or industrial facility, today’s tariff-driven environment can feel daunting. Rising steel costs may affect everything from your project timeline to your final invoice. Here are some strategies to help you navigate these market shifts with confidence:
Discuss Project Scope in Advance
Whether you’re adding an extra bay to your garage or customizing a warehouse layout, defining your needs from the start can limit mid-project changes—and the associated cost increases that come with design revisions.
Consider Bundling Construction Services
If your building partner offers bundled services—like site prep, slab work, and erection—this can sometimes reduce total labor and overhead costs compared to hiring multiple vendors. It also simplifies logistics, which is especially helpful in a volatile pricing environment.
Ask About Financing or Phased Construction
For larger projects, whether residential or commercial, look into financing options or a phased construction approach. Spreading out the build or financing it can ease the immediate financial burden if steel prices remain elevated.
Build Relationships with Trusted Providers
A reliable contractor or supplier can offer valuable insights into timing your purchase, exploring alternative materials, and making design tweaks that minimize cost. Communication and transparency are critical; don’t hesitate to ask for up-to-date pricing data or clarification on any fees in your estimate.
Plan for Potential Delays
Tariffs and supply chain issues can sometimes slow down the delivery of raw materials. If your timeline is tight—whether it’s a personal workshop that must be done before winter or a commercial site with tenants lined up—factor in a buffer to accommodate possible shipment delays or backlogs at the mill.
By focusing on clear communication, flexible planning, and proactive decision-making, both private buyers and commercial operators can mitigate the financial impacts of rising steel prices. In a market driven by global events and swift policy changes, preparedness is your best ally—whether you’re putting up a cozy luxury barndominium or an expansive manufacturing facility.
Looking Ahead: How 2025 Could Shape the Future
While the immediate future points to rising costs for metal buildings, it’s worth noting that markets have a way of finding new equilibrium over time. If domestic producers increase capacity, competition may stabilize prices. If international trade policies shift in a friendlier direction, imports could become less expensive again. In any scenario, however, the events of 2025 underscore how pivotal global trade relations and supply chain resilience are to the construction and manufacturing sectors.
In this environment, it’s wise to remain cautious yet proactive:
- Monitor Policy Shifts: Changes at the federal level—whether in Washington, D.C. or in major steel-exporting nations—can dramatically alter price forecasts. The U.S. International Trade Commissionregularly publishes findings that shed light on steel import regulations and potential policy changes. Staying informed helps you time purchases or finalize building plans ahead of any sudden price hikes.
- Invest in Innovation: Whether you’re a farmer adding a barndominium for equipment storage or an entrepreneur planning to expand your retail, commercial, or self-storage space, now is the time to explore alternative building techniques and energy-efficient designs. For example, adding insulation, solar-ready roofing, or modular components can reduce long-term operating costs and enhance a building’s versatility. Innovative design choices—like flexible interiors that adapt to future needs—may require more forethought but can yield both cost savings and improved functionality over the life of the structure.
- Diversify Products and Markets: Farmers might consider using their new metal building for both storage and on-site agritourism activities, while smaller commercial developers could transform a single-purpose warehouse into a mixed-use facility with coworking areas or retail pop-ups. By expanding how buildings are utilized—or broadening the types of structures you invest in—you spread financial risk across multiple revenue streams or operational functions. This approach also keeps you agile if steel prices spike further or if policy changes open up new opportunities.
Conclusion
The newly implemented 25% global tariff on steel and aluminum—along with potential anti-dumping rulings and coil-coating inflation—heralds a period of uncertainty for the metal building industry. Yet, it’s also a moment for businesses and builders to show their adaptability. By staying informed, investing in flexible strategies, and communicating openly with partners and clients, companies can navigate the rocky waters of 2025 without losing momentum.
Metal buildings remain a cornerstone of modern construction, prized for their durability, speed of assembly, and design versatility. Even amid unpredictable price changes, organizations that plan carefully and remain agile will continue to harness the immense value steel provides.
SteelCo has 20+ years of supplying custom PEMB materials and commercial general contracting expertise taking your projects from concept and design all the way to completion and “certificate of occupancy”. Learn more about our experience in steel building design and metal buildings.